Sign in to follow this
Followers
0
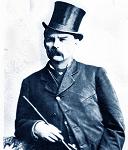
MS type AI Progress
By
Bullethead, in WOFF 1 2 3 / UE - Skinning / Modeling Help
By
Bullethead, in WOFF 1 2 3 / UE - Skinning / Modeling Help
By using this site, you agree to our Terms of Use, Privacy Policy, and We have placed cookies on your device to help make this website better. You can adjust your cookie settings, otherwise we'll assume you're okay to continue..